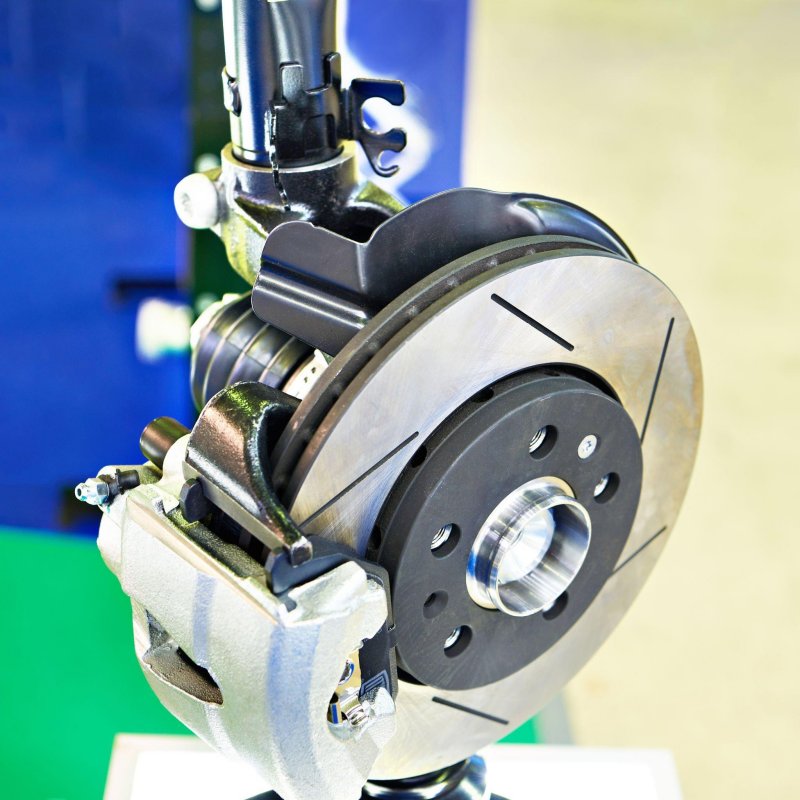
High-Fatigue Life Disc Springs for Critical Machinery
Application:Specialized for customization according to customer requirements, with high rigidity.
Design team and technical team: Our design and technical experts collaborate to provide innovative and meticulously crafted products for clients. We specialize in spring design,manufacturing, and optimization.
One-stop service: Zhejiang Yurong Spring Co., Ltd. builds its own brand in terms of management mode, quality management, and brand image, earning trust and reliability.
Introduction to High-Fatigue Life Disc Springs
Disc springs are widely used in critical machinery applications to provide flexibility, absorb shock, and maintain proper load distribution. However, in industries where continuous operation is essential, such as power plants or aerospace, fatigue failure of disc springs can lead to costly downtime and potential safety hazards. To address this issue, engineers have developed high-fatigue life disc springs that offer improved durability and reliability, ensuring uninterrupted functioning of critical machinery.
Understanding the Challenges of Fatigue Failure
Fatigue failure in disc springs occurs due to repeated loading and unloading cycles, causing the material to weaken over time. Factors such as excessive stress, improper design, or material defects can accelerate this fatigue process, leading to premature failure. For critical machinery applications, where the springs are subjected to high loads and continuous operation, it becomes crucial to mitigate the risk of fatigue failure through the use of high-fatigue life disc springs.
Innovative Design and Material Considerations
To enhance the fatigue life of disc springs, engineers employ innovative design techniques. This includes optimizing the number of turns, thickness, and curvature of the disc springs to ensure a balanced load distribution. Additionally, material selection plays a vital role in improving fatigue resistance. High-quality alloys with enhanced mechanical properties, such as chrome-vanadium or stainless steel, are often preferred for manufacturing high-fatigue life disc springs.
Manufacturing Processes for High-Fatigue Life Disc Springs
Manufacturing high-fatigue life disc springs requires stringent quality control measures to ensure consistent performance. Advanced heat treatment techniques, such as shot peening or stress relieving, are employed to enhance the material's fatigue resistance and prevent stress concentration. Precision machining and surface finishing techniques also play a crucial role in achieving the desired dimensional accuracy and smoothness, which further contribute to the durability of high-fatigue life disc springs.
Performance Benefits and Applications
The use of high-fatigue life disc springs in critical machinery applications brings numerous performance benefits. These springs offer extended service life, minimizing the need for frequent replacements and reducing maintenance costs. Additionally, their improved fatigue resistance enhances the overall reliability of the machinery, reducing the risk of unexpected failures. High-fatigue life disc springs find applications in various industries, including power generation, oil and gas, automotive, and aerospace, where uninterrupted operation is paramount.
Future Developments and Conclusion
As technology advances, engineers continue to explore new materials, design techniques, and manufacturing processes to further enhance the fatigue life of disc springs. Ongoing research focuses on developing advanced alloys with superior fatigue resistance and exploring innovative spring geometries to optimize load distribution. With the continuous evolution of high-fatigue life disc springs, critical machinery can operate with increased efficiency, improved safety, and reduced downtime, ensuring the seamless functioning of vital industrial processes.